When the Gears Stopped Turning at a Local Farm, DU Stepped In
With no manuals, no parts, and no instructions, engineering student Uton Delloso reverse-engineered a decades-old gearbox to get the farm’s irrigation system running again.
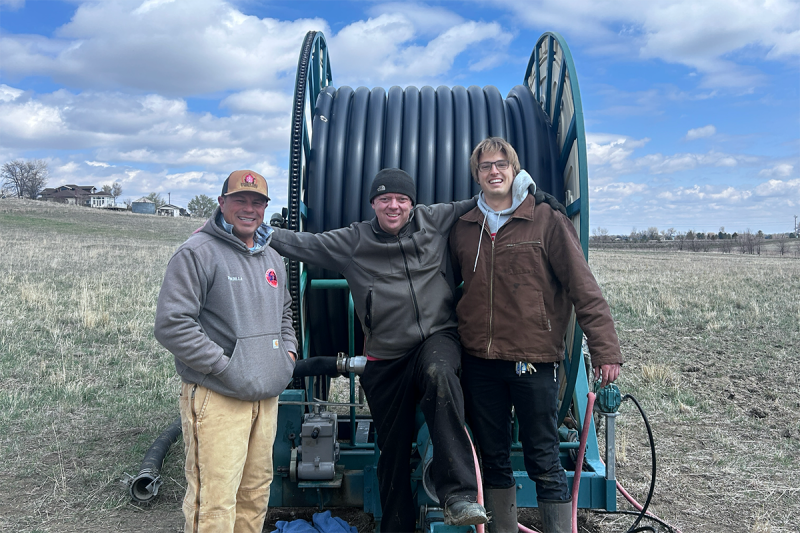
An employee (left), Justin Huff (center), and Uton Delloso (right) standing in front of the repaired irrigation system.
Has your car ever been stuck at the mechanic waiting on an out-of-stock part? Or maybe your laptop repair is delayed because the replacement components are stuck in a warehouse overseas.
Supply chain issues aren’t just inconveniences for consumers—they can bring essential work to a halt. That’s what happened at the Olson family farm near Longmont, Colorado, when a decades-old irrigation system broke down. A critical gearbox failed, and no replacement part existed. It was long out of production, with no manuals and no manufacturer support.
That’s when Justin Huff, mechanical lab manager in the Ritchie School of Engineering and Computer Science, got the call. Huff oversees DU’s Machine Shop, a hands-on workspace where students from all majors learn to use industrial tools—mills, lathes, saws, and more—to bring their ideas to life. A farm employee discovered the shop after reading an article about it online and reached out, hoping someone at DU might be able to help. The request wasn’t simple—no instructions, no blueprints, and a gearbox full of broken pieces. But Huff saw it as an opportunity.
“It was a bad day. Big noise, big boom, crack, everything stopped moving. Their employee had called a bunch of machine shops in Denver and Longmont, trying to find someone who would take a look at it and see if they could fix it. But no one was willing to take a jab at it,” Huff says.
Though Huff didn’t have time to take on the project by himself, he knew someone who might. He shared the idea with Uton Dellosso, a fourth-year mechanical engineering student. Last summer, the duo completed repairs on the Chamberlain Observatory’s rotating mechanism.
“They sent a couple pictures, and I told Uton, ‘If you're interested, this is going to be your project,’” Huff says.
When the gearbox arrived at DU, it was a mess—three gears had shattered, leaving the entire system inoperable.
Disassembly alone was a challenge. The gearbox, Italian-made, was so old that even the original manufacturer no longer recognized it.
“It’s like someone gave you a Lego set and said, ‘I want you to take this specific piece out,’ and you’ve got to figure it out with no instructions,” Dellosso says.
After two weeks of trial and error, Dellosso managed to extract the damaged gears. They shipped the pieces, along with one intact spur gear for reference, to Moore Machine & Gear, a fabricator in Indiana that Huff had worked with during graduate school.
The fabricator was able to make new gears and, once they arrived, the repair came together fast. Huff was planning for a three-week rebuild, but “Uton slapped it together in about an hour and had it spinning. We went up to Ace, got some paint, and gave it a new paint job,” he says.
For Dellosso, the process was an exciting challenge and an opportunity to expand his engineering knowledge and machining skills. “I was very impressed with the people that made the gears. They're dead accurate, and they didn't have much to work on. It was cool to see how they were able to reverse engineer the gear box and fabricate new parts.”
Seeing the gearbox with a fresh coat of paint was rewarding, but the project really came full circle when they spent a weekend at the farm installing the gearbox in March. “That was a nice ‘it's all come together’ moment,” Dellosso says.
Huff says he’s always excited to see students from all backgrounds show up at the shop, eager to learn—and often ready to teach a few things themselves. That kind of exchange, he says, is what the space is all about.
“I always tell them, I’ll teach your grandma how to run those machines. I don’t care who you are—I just want you to come in here, have fun, and be safe.”
Interested students—from any major—can sign up for the Machine Shop Practice class in the summer to learn how to use the mill, lathe, band saws, and more. With a machine shop certification, students can use the machine shop for academic and personal projects.